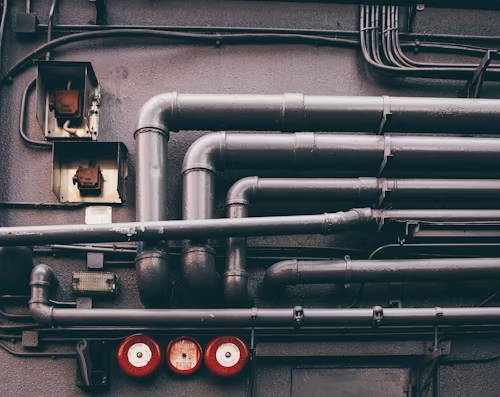
Galvanized Iron (GI) pipe fittings are a fundamental component in Malaysia’s industrial infrastructure, providing durable and efficient conduits for fluid and gas transport in numerous sectors. Their robustness and resistance to corrosion make them ideal for a range of industrial muliatoto applications. This article explores the best practices for installing GI pipe fittings Malaysia in industrial systems, ensuring optimal performance and longevity.
Understanding GI Pipe Fittings
GI pipe fittings are made from steel pipes that have undergone a galvanization process, which involves coating them with a layer of zinc to prevent rust and corrosion. This makes them particularly suitable for industrial environments sultantoto where exposure to moisture and chemicals is common. They are used in a variety of applications, including water supply, waste management, and in oil and gas industries.
Pre-Installation Planning
Site Assessment: Before installation, conduct a thorough assessment of the site to understand environmental factors, the chemical composition of fluids being transported, and pressure requirements. This helps in selecting the right type and size of fittings.
System Design: Design the piping mastertoto system to minimize pressure drops and ensure smooth flow. Consider the layout for ease of maintenance and inspection. Ensure that all components are accessible.
Installation Techniques
Proper Handling: GI fittings should be handled with care to avoid damaging the zinc coating, which could lead to rust formation. Ensure that the fittings are stored in a dry area before installation to prevent premature corrosion.
Cutting and Threading: When cutting GI pipes to length, use sharp, proper tools to make clean cuts. Clean all burrs from cut pipe ends and properly thread them to ensure a tight and secure fit. Use appropriate threading dies and cutting oils.
Joining Methods: GI pipe fittings can be connected by threading, welding, or using mechanical youngtoto joints. Choose the method based on the system’s pressure requirements and the fluid type. For most industrial applications, threading is sufficient and provides a reliable seal.
Sealing: Use high-quality presidenttoto thread sealants suitable for galvanized piping to prevent leaks. Teflon tape or pipe dope can be applied to threaded joints to enhance the seal.
Testing and Commissioning
Pressure Testing: Once installation is complete, perform pressure testing to check for leaks. Use water or another suitable testing medium at higher pressures than the system will operate to ensure safety and reliability.
System Flush: Flush the system to remove any debris or contaminants from installation that could clog or damage the system components.
Maintenance and Monitoring
Regular Inspections: Schedule regular inspections to check for signs of wear, corrosion, or leakage. Pay special attention to joints and fittings.
Corrosion Protection: Even though GI fittings are galvanized, they can still corrode over time, especially at threaded joints. Apply protective paints or direkturtoto additional coatings if necessary, especially in highly corrosive environments.
Documentation: Keep detailed records of all maintenance activities, inspections, and replacements. This documentation is crucial for understanding the sultantoto lifecycle of the piping system and planning future upgrades or replacements.
Conclusion
Installing GI pipe fittings in industrial systems in Malaysia requires careful planning, precise installation techniques, and ongoing maintenance to ensure the muliatoto system’s integrity and performance. By following these best practices, industries can maximize the benefits of their GI piping systems, ensuring safe and efficient operations.